在现代化的工业生产中,
减震器疲劳试验机起着至关重要的作用。这款设备广泛应用于各类产品的性能测试和质量控制,尤其在汽车、航空航天、电子产品等领域。为了确保生产效率和产品质量,减震器疲劳试验机的正常运行是关键的。因此,对其可能出现的故障进行智能诊断和预警,对生产过程的顺利进行具有重要意义。
一、智能故障诊断
传统的故障诊断方法依赖于人工经验,但这种方式存在一定的局限性,如诊断准确度不高、处理速度慢等。随着人工智能技术的发展,智能故障诊断逐渐成为了主流。利用大数据、深度学习等技术,可以实现对设备运行数据的实时监控和深度分析。一旦发现异常数据,系统就会自动诊断并发出警报,从而提早发现潜在问题。
具体来说,智能故障诊断的实现步骤如下:
1.数据收集:通过在设备上安装各种传感器,收集运行过程中的压力、温度、振动等关键数据。
2.数据处理:将收集到的数据进行预处理,如去噪、归一化等,以提高分析准确性。
3.特征提取:从处理后的数据中提取出反映设备运行状态的特征,如频谱分析、时域分析等。
4.模型训练:利用提取的特征训练深度学习模型,建立设备正常运行和故障运行的数据库。
5.故障诊断:将实时监控到的数据输入训练好的模型进行比较,判断设备当前状态,一旦发现异常,即发出警报。
二、智能预警
减震器疲劳试验机的智能预警系统基于其运行数据和可能出现的故障模式进行预警。通过对设备历史数据的分析,可以预测其未来可能的性能变化,从而提前采取措施防止故障发生或降低故障对生产的影响。
智能预警的实现步骤如下:
1.数据存储:将设备的历史运行数据存储在数据库中,以便进行数据分析和模型训练。
2.数据分析:利用大数据技术对历史数据进行深入分析,发现隐藏在其中的故障模式和规律。例如,通过分析设备在各种工况下的性能变化,可以建立起更加精确的设备性能预测模型。
3.模型训练:利用分析得到的数据,训练预测模型,并根据实际运行数据进行不断优化和调整。
4.实时监控:通过实时接收设备的运行数据,对模型进行验证和校准,确保预警的准确性。
5.预警输出:一旦模型预测到设备可能出现故障或性能下降,即发出预警信号,提醒操作人员采取相应措施进行干预,从而降低生产过程中的停机时间和损失。
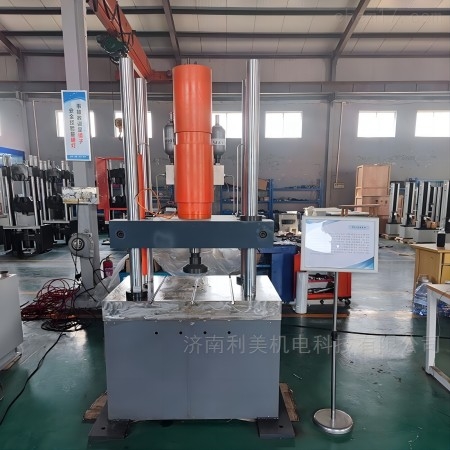
总之,通过智能故障诊断和预警技术,可以实现对设备的实时监控和预防性维护,提高设备的运行效率和可靠性,保障生产过程的顺利进行。这些技术的应用不仅提高了企业的生产效率,也降低了设备的维修成本,为企业创造了更大的经济效益。